HTAN is one of the leading manufacturers of industrial hinges, handles and latches in China.
-
+86 13720060320
-
julius@haitangs.com

Cam Latch or Compression Latch – What’s the Difference and Which to Choose?
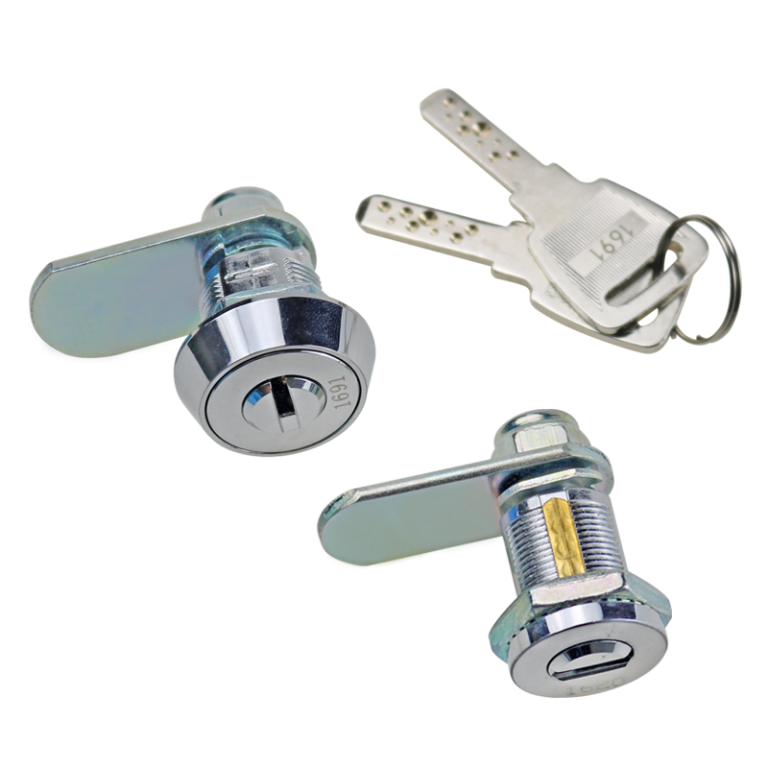
If you are designing industrial equipment, cabinets or outdoor enclosures, choosing the right latch (Cam Latch or Compression Latch) is directly related to the security, sealing and longevity of the equipment.
The wrong choice can lead to loose door panels, rainwater infiltration, or even equipment accidentally opening during vibration.
What is Cam Latch?
Principle of Construction and Operation
Cam Latch is a mechanical rotary latch.
Its core component is a rotatable metal cam (usually 90° or 180°).
When the handle is rotated, the cam will snap into the door frame or corresponding groove to complete the locking action.
Features
- Typically only 1/4 turn rotation is required for quick unlocking
- Simple structure with fewer parts
- Supports push-pull or toggle operation
Typical Application Scenarios
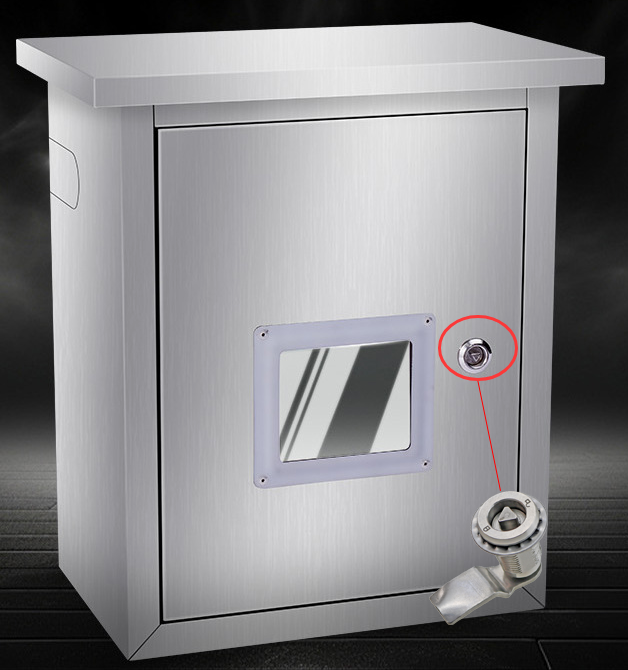
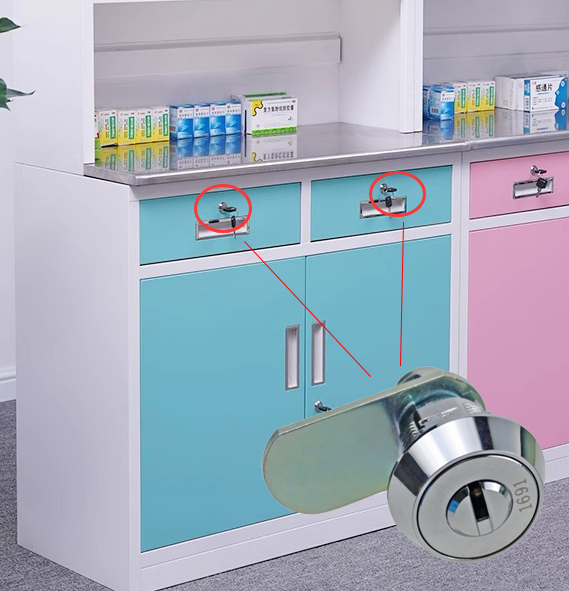
- Electrical control cabinet/distribution box: Frequent maintenance of electrical control equipment, need to lock and unlock quickly.
- PLC control cabinet: industrial production line equipment maintenance, saving downtime.
- Frequency converter / servo drive enclosure: convenient maintenance of internal circuit modules.
- Network cabinet/server cabinet: high-frequency equipment inspection and heat dissipation maintenance.
- 5G Base Station Equipment Enclosure: Quickly overhaul communication modules in mild outdoor climate.
- Edge computing terminal: simplify the deployment and maintenance process of edge devices.
Summary
- Low cost
- Easy installation (standard openings, no need for complex commissioning)
- Fast operation (suitable for multiple switching scenarios per day)
What is Compression Latch?
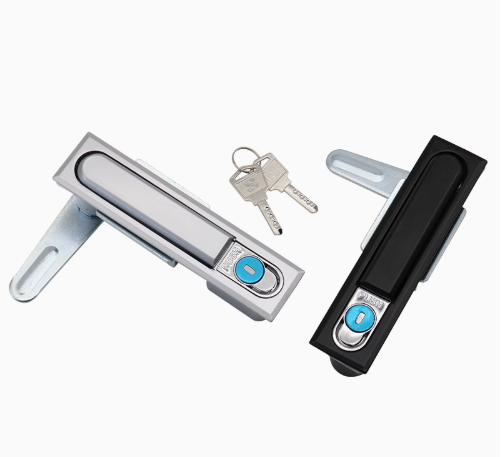
Principle of Construction and Operation
The Compression Latch adds a pressure adjustment mechanism to the basic locking function.
By means of a spring or threaded structure, vertical pressure is exerted on the door panel during locking to ensure a tight fit between door and frame.
Features
- Two-stage operation: locking, then compression (usually requires 1-2 turns)
- Built-in sealing gasket (made of EPDM or silicone)
- Adjustable pressure level (some models support torque adjustment)
Typical Application Scenarios
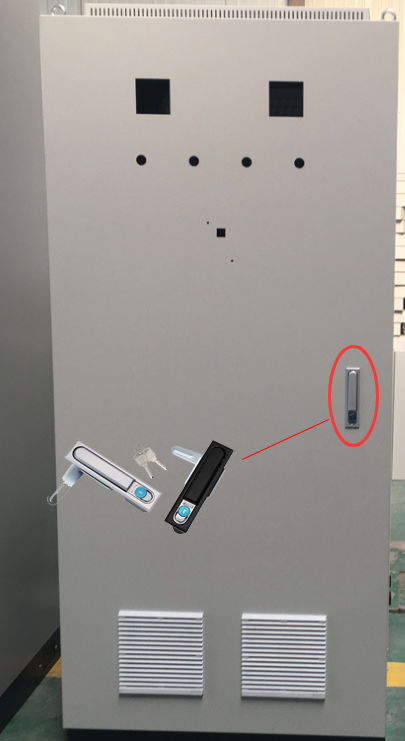
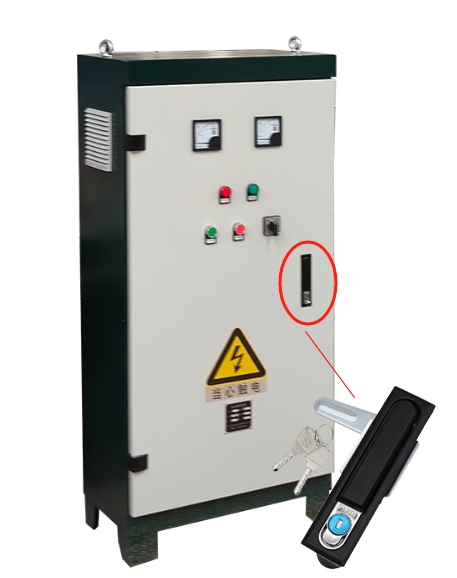
- Heavy duty cabinets/power distribution cabinets: high load securing in industrial environments, vibration and corrosion resistant.
- Machine tool guard doors: quick locking/unlocking for operational safety.
- Hydraulic/pneumatic equipment housings: efficient maintenance under frequent maintenance requirements.
- Control panels for automated production lines: anti-touch design reduces the risk of downtime.
- Medical equipment transportation case: anti-vibration sealing design to ensure safe transportation of precision instruments.
- Biological sample storage cabinets: high load-bearing latches, suitable for low-temperature environments.
- Laboratory fume hoods: quick opening and closing for emergency operation.
- Centrifuge/sterilizer enclosure: corrosion-resistant material, in line with clean standards.
Summary
- Superior sealing
- Vibration-resistant design
- Long life cycle
Key Differences between Cam Latch and Compression Latch
Sealing Performance Comparison
- Cam Latch: provides basic locking only, with a possible 0.5-1mm gap in the door.
- Compression Latch: Zero gap sealing through compression gaskets, supports IP67/IP69K protection rating.
Anti-vibration Capability
- Cam Latch: May loosen during vibration above 15Hz.
- Compression Latch: Pre-tensioned design counteracts 80% of vibration energy.
Mounting Complexity
- Cam Latch: Standardized mounting holes (e.g., 12mm round holes), 5 minutes to assemble.
- Compression Latch: Panel thickness and compression stroke need to be calculated.
Operation Experience
- Cam Latch: One-handed operation, suitable for gloved hands.
- Compression Latch: requires more force to operate
Maintenance Requirements
- Cam Latch: check tongue wear every 6 months.
- Compression Latch: check spring force and seal deterioration every 3 months.
Key Decision Points
Evaluate Environmental Harshness
- High humidity/dusty environments: prioritize Compression Latch
- Dry, clean room: Cam Latch is more economical.
Calculate Switching Frequency
- 10 switches per day: Cam Latch is mechanically more durable.
- <5 switches per week: Compression Latch offers sealing advantages.
Measuring Panel Thickness
- Panel thickness <2mm: choose Cam Latch
- Panel thickness 3-6mm: Compression Latch can be adapted.
Determine the Level of Security
- Basic anti-theft requirements: Cam Latch + padlock is sufficient.
- Anti-breaking and explosion-proof needs: Compression Latch + three-point locking system.
FAQ
Q1: Can Compression Latch be used for indoor equipment?
Yes, with two caveats:
- The compression gasket may deteriorate faster if the indoor humidity is below 60%.
- When there is no need for waterproofing, it is recommended to turn off the compression function to prolong the life of the gasket.
Q2: How do I choose the right latch for my panel thickness?
Measure the total thickness of the door panel (including the seal).
Select a model with a travel range covering “thickness + 1mm” (e.g. 4-5mm travel for 3mm panel).
Q3: Is Cam Latch waterproof?
The standard Cam Latch is not waterproof. However, it can be improved to IP44 protection by the following:
- Adding a silicone sleeve to the swivel tongue
- Adhesive sealing foam on the inside of the door frame
Installation and Maintenance Recommendations
Installation Considerations
- Cam Latch: Make sure that the cam rotates in the same direction as the door opens.
- Compression Latch: It is recommended to set the pre-compression force to 70% of the maximum value (to prevent over-compression of the seal).
Routine Maintenance Procedures
- Quarterly check: Test the Compression Latch with a manometer to check for compression force decay.
- Annual maintenance: Apply silicone-based grease to the Cam Latch shaft.
- Emergency: If the Compression Latch fails to compress, clean the threads before adjusting the preload nut.
Conclusion
There are no absolute advantages or disadvantages between Cam Latch and Compression Latch.
Cam Latch is suitable for cost-conscious, operationally efficient general purpose applications, while Compression Latch is the preferred choice for safety and sealing in harsh environments.