HTAN is one of the leading manufacturers of industrial hinges, handles and latches in China.
-
+86 13720060320
-
julius@haitangs.com

Heavy-Duty Hinges: A Complete Engineering Guide for Industrial Use
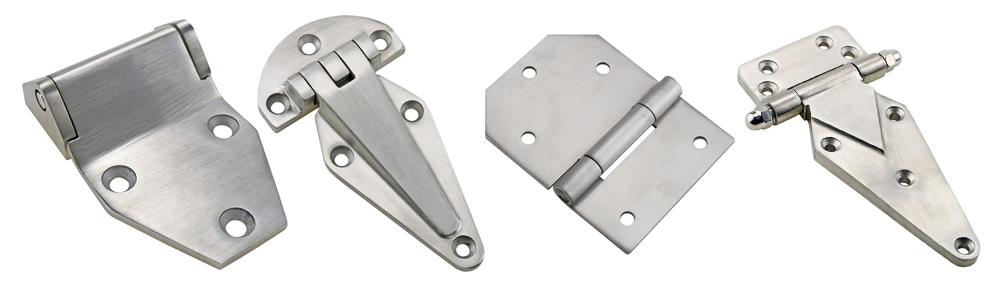
In modern industry, from warehousing and logistics to data centers, cold chain facilities to offshore platforms, heavy-duty hinges play a critical role. These robust hinges must handle not just the door’s weight, but also frequent operation, heavy impacts, and harsh environments.
Studies show that using commercial-grade heavy-duty hinges can:
- Slash replacement costs by ~60%
- Reduce maintenance calls by 73% over five years
- Minimize equipment downtime and accident risks
Yet, diverse application needs demand multi-dimensional evaluation—across load capacity, corrosion resistance, lifespan metrics, and regulatory compliance (OSHA, CE, ATEX). This ensures:
- Lower lifecycle costs (-30%)
- Reduced maintenance frequency (-50%)
- Regulatory adherence
This article builds a systematic heavy-duty hinge selection methodology. Focused on technical specs, not brand endorsements, it empowers corporate decision-makers to achieve optimal hinge selection through quantitative analysis.
Read on to master a proven process—from scenario profiling to performance validation—significantly improving the science and reliability of heavy-duty hinge selection .
Defining Heavy-Duty Hinges & Key Performance Indicators
Heavy-duty hinges are engineered for loads exceeding standard doors. Their specifications far surpass household hinges.
Industry benchmarks:
- ANSI/BHMA A156.1 Grade 1: 2.5 million cycles
- ASTM B117: Salt spray corrosion testing
- Static load: >200 kg per hinge
Key Performance Dimensions
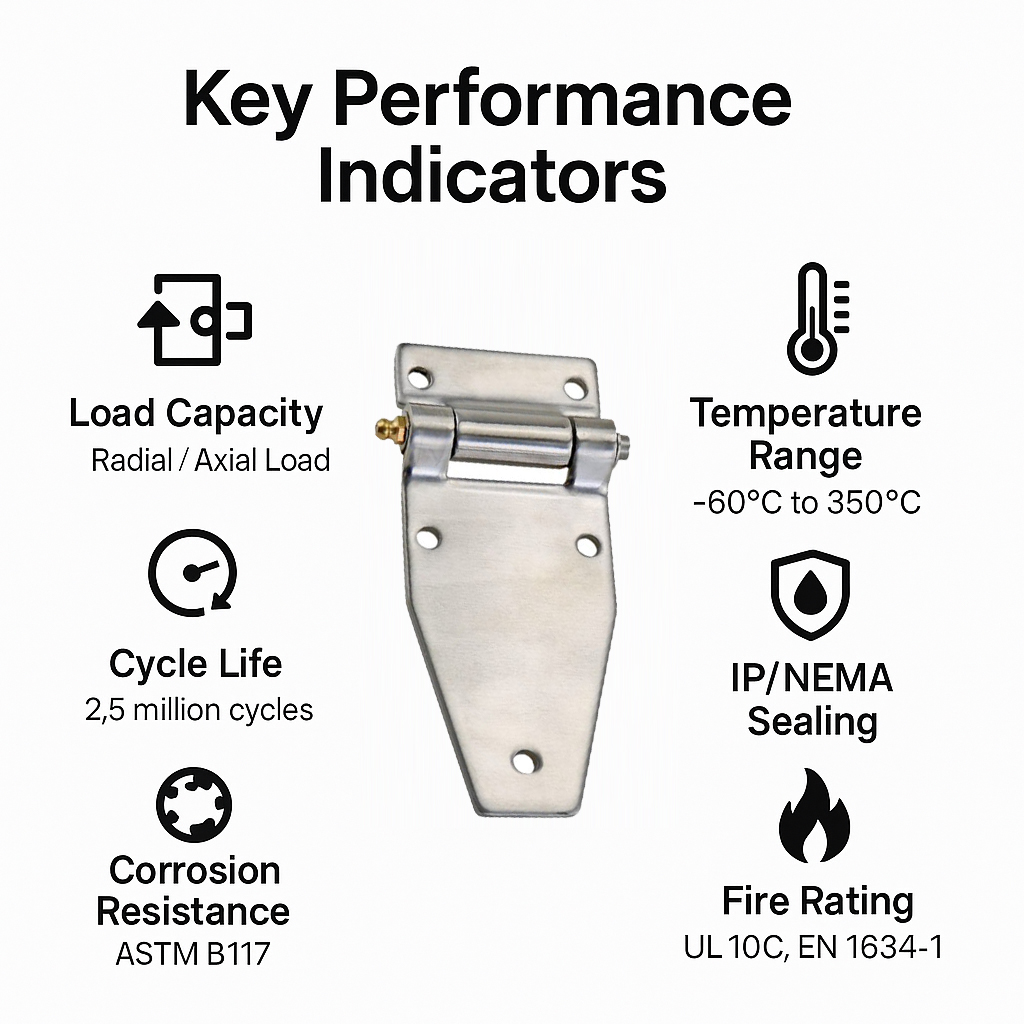
- Load Capacity: Radial, axial, and combined
- Cycle Life: Lab-tested and field-equivalent
- Corrosion Resistance: ASTM B117, ISO 9227 CASS
- Temperature Range: -60°C (-76°F) to 350°C (662°F)
- Sealing: IP/NEMA/explosion-proof ratings
- Fire Rating: UL 10C, EN 1634-1 certifications
Always verify supplier quality management (e.g., ISO 9001) and product certifications (e.g., DIN EN 1935, ANSI/BHMA A156.1).
Industrial & Commercial Application Profiles
High-Frequency Use Cases
Logistics: Loading Dock Doors
- Withstand hundreds of cycles/day & forklift impacts
- Heavy-duty hinges absorb collision energy
- Poor hinges cause door detachment, downtime, and safety issues
Pharma/Semiconductor: Cleanroom Air-Lock Doors
- Airtightness >±50 Pa pressure
- Meet GMP/ISO standards
- Stainless steel finish & continuous grounding prevent EMI and contamination
Offshore Wind Turbine Access Doors
- Face salt spray, UV, vibration
- Materials: 2205 duplex SS, special alloys
- Coatings: Weatherproof + DLC (low-friction)
- Result: 5+ years maintenance-free
Data Center Cabinet Doors
- Require EMI shielding & grounding
- Hinges provide structural and electrical support
- Ball-bearing type ensures high-cycle silent operation
Freezer/Cold Storage Doors
- Operate below -30°C (-22°F)
- Use 316L SS + PEEK bushings + cryo lubricants
- Result: Failure rate drops from 5% → 0.3% per year
Mapping Needs to Specifications
Industry | Hinge Priority |
---|---|
Logistics | Load capacity & cycle life |
Cleanrooms | Sealing & corrosion resistance |
Offshore | Salt spray & fatigue resistance |
Data Cabinets | Electrical conductivity & EMI shielding |
Cold Storage | Low-temp toughness |
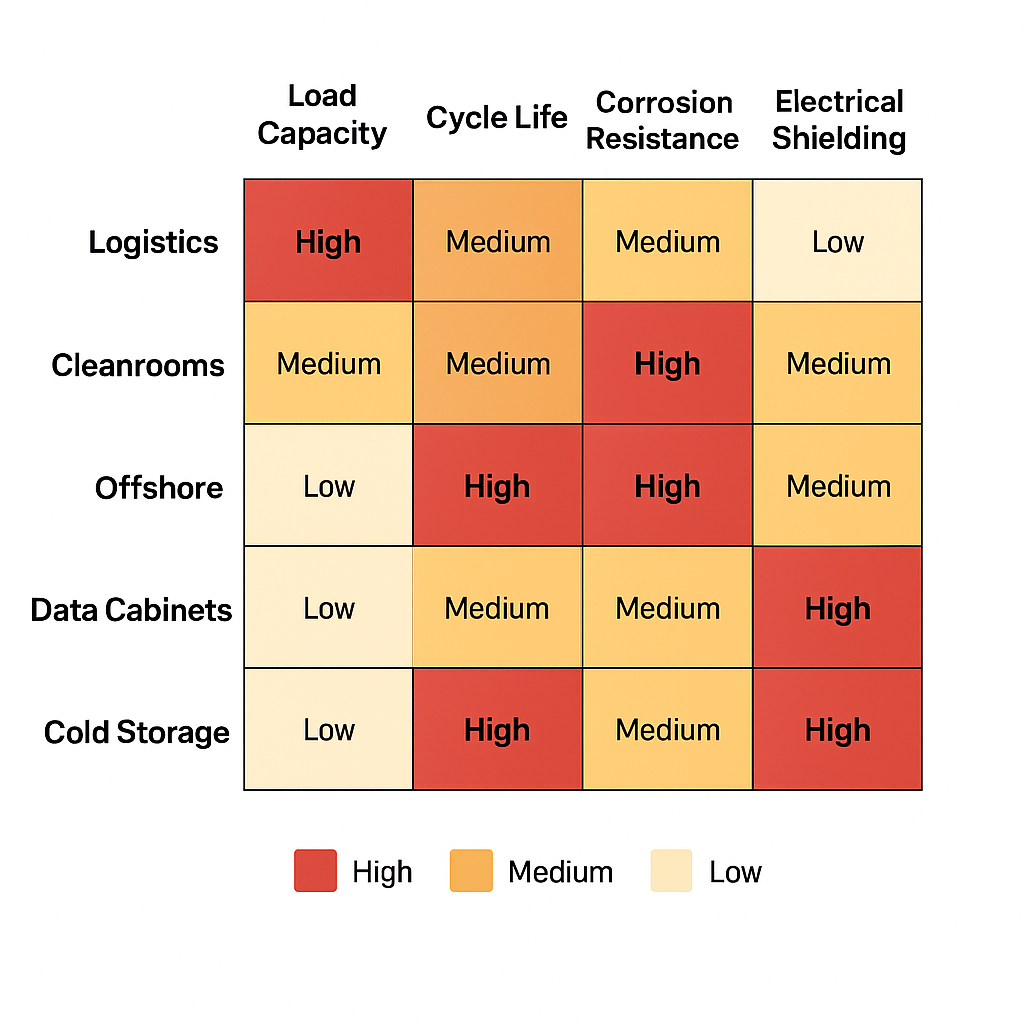
Material & Manufacturing Deep Dive
Metals
- C1045 Carbon Steel: High strength + plating required
- 304 SS: Cost-effective, decent corrosion
- 316L SS: Marine-grade, added Molybdenum
- 2205 Duplex SS: 2× yield of 316L, best in chlorides
- 7075-T6 Aluminum: Aerospace-grade, 50% weight reduction, requires anodizing
Non-Metals & Composites
- PEEK Bushings: Ultra-low friction, -70°C stability
- Carbon Fiber Epoxy: 40–60% lighter than steel, ideal for trains
Manufacturing Processes
- Forging > Casting: Stronger, better fatigue strength
- 5-Axis CNC: Precision ±0.02 mm
- MIM: Cost-effective for complex shapes, cuts costs 20–25%
Surface Engineering
- Dacromet + PTFE: >2000 hrs salt spray resistance
- DLC Coating: μ=0.1–0.2, cold-temp dry-running smoothness
Hinge Types & Installation
Common Structures
Hinge Type | Key Feature | Benefit |
---|---|---|
Butt Hinges | Strongest load-bearing | Ideal for heavy industrial doors |
Piano Hinges | Full-length support | Distributes weight evenly along the edge |
Weld-On Hinges | No loosening, high strength | Permanent, vibration-resistant solution |
Lift-Off/Bolt-On | Easy door removal | Tool-free maintenance and quick access |
Adjustable Hinges | ±3 mm adjustment | Allows post-installation fine-tuning |
Concealed vs. Exposed | Aesthetics vs. access | Hidden for clean look; exposed for ease of service |
Installation Accessories
- Reinforcement plates
- EPDM/silicone seals
- Grounding straps for EMI/ESD protection
Load Calculation & Life Prediction
Static Load
- Use 3-point load models + FEA
- Include safety margin
- Example: 100kg door → 240kg hinge load (4:1 SF)
Dynamic & Impact Loads
- Docks/wind → 5× static load
Fatigue Life
- Use S-N curves + Miner’s Rule
- Industrial: 4:1 SF, Aerospace: 8:1 SF
- Rated cycles must far exceed design life
Tools
- Excel/Python calculators
- Input: weight, hinge count, angles
- Output: Verified hinge selection
Environment & Regulatory Compliance
Harsh Environment Mitigations
- Salt Spray: Sacrificial Mg/Zn anodes
- Dust: Labyrinth seals
- High Temp: Graphite lubricants
- Low Temp: Cryo grease (-60°C)
Key US Regulations
- OSHA: ≥3mm radii, pinch-prevention
- NFPA 80: Fire door hinge count rules
- ATEX: Use non-sparking (e.g., CuBe alloy) in Zone 1+
Cost & Supply Chain Strategy
Factors Affecting Total Cost of Ownership (TCO):
- Purchase Price
- Installation
- Maintenance/Repair
- Downtime
Strategies
- High-Quality Hinges → Lower TCO
- Modular Design: Standard parts reduce SKUs by 40%
- Global Sourcing:
- Germany: Precision
- China: Lead time/volume
- USA: Specialty/custom
- Specify MOQ, tolerances, RoHS/REACH
Case Studies
Cold Storage Logistics Center
- Temp: -25°C, 500 cycles/day
- Problem: Frost jamming
- Solution: 316L SS + PEEK + heaters
- Result: Failure rate → 0.3%/yr
Offshore Wind O&M Platform
- Problem: Salt, UV, vibration
- Solution: 2205 SS + DLC + weld-on
- Result: 5+ years no service, -50% maintenance dispatches
Semiconductor Cleanroom
- Specs: ISO 100, ESD, 50Pa
- Solution: Conductive hinges + seals
- Result: -30% particles, 0 ESD incidents
Maintenance & Troubleshooting
Preventive Schedules
- General: Every 6 months
- Cleanroom: Every 3 months
- Offshore: Monthly
IoT Smart Hinges
- Monitor: Cycles, angles, stress
- Communication: LoRaWAN
- Benefit: Predictive maintenance
Troubleshooting (FTA)
- Common issues: Noise, sagging, corrosion
- Check: Lubrication, alignment, wear
- Solutions: Replace bushings, re-coat, weld
Rapid Field Repair
- Techniques:
- Pressurized grease
- Shim gaps
- Laser cladding (restoration)
Conclusion & Action Plan
3-Step Selection Methodology
- Profile the Scenario: Define load, environment, cycles, regulations
- Quantify Specifications: Match KPIs (load, life, corrosion, etc.)
- Validate: Lab + field testing
FAQ
When are heavy-duty hinges needed?
Use them for doors over 110 lbs, high-frequency use, extreme environments (shock/vibration/temperature), or special needs like corrosion resistance/EMI sealing.
Key specs for heavy-duty hinge selection?
Prioritize: Load capacity, lifecycle cycles, corrosion rating (ASTM B117/ISO 9227), temperature range (-60°C to 350°C), and certifications (UL/EN/ATEX).
How to calculate load capacity?
Design for 4x the door’s weight (industrial standard). Allow 5x static load for dynamic impacts. Verify with FEA analysis.
Industry-specific requirements?
Cold Chain: Sub-zero materials (-30°C)
Pharma: Sealed/sterile design
Data Centers: EMI shielding
Offshore/Wind: Salt-resistant coatings + vibration tolerance
Reducing maintenance costs?
Use forged hinges with low-friction bushings, schedule preventive maintenance, install IoT-monitored smart hinges, and choose modular designs for easy part swaps.