HTAN is one of the leading manufacturers of industrial hinges, handles and latches in China.
-
+86 13720060320
-
julius@haitangs.com

Cam Latch Installation Guide
Cam Latch is a quick latching device that is widely used in scenarios such as electrical control cabinets, industrial equipment enclosures, and transportation cargo holds.
Its core function is to generate pressure through a rotating cam structure to seal and secure.
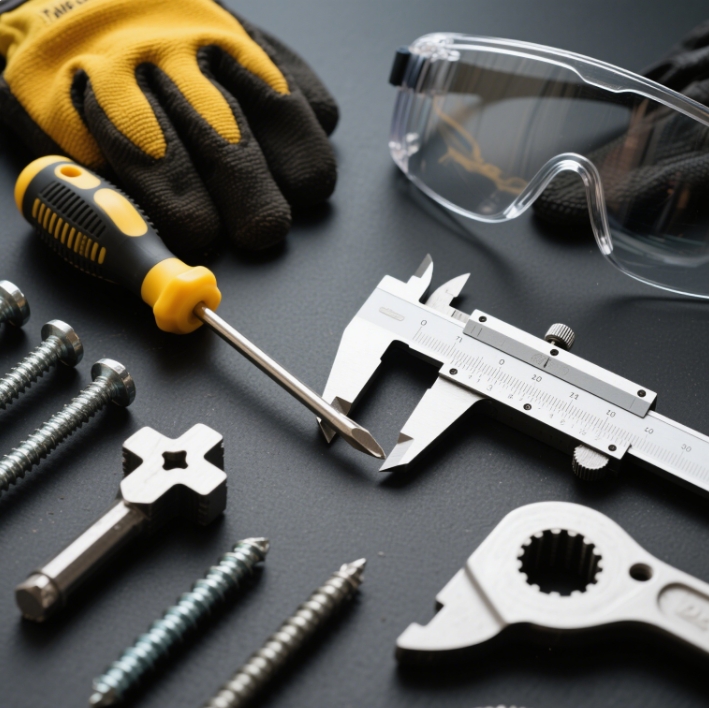
Preparation before Installation
Tools and Safety Equipment List
Necessary tools: Phillips screwdriver, vernier caliper, hole opener
Protective equipment: cut resistant gloves, goggles
Parameters that Must Be Confirmed
Cabinet Material:
Aluminum alloy/steel plate: use HSS cobalt steel hole opener
Engineering plastics: It is recommended to drill and test the holes first to avoid material cracking
Thickness Measurement:
Measure the cabinet thickness with vernier calipers in at least 3 positions
IP Protection Requirements:
IP65 rating with EPDM waterproof gasket required.
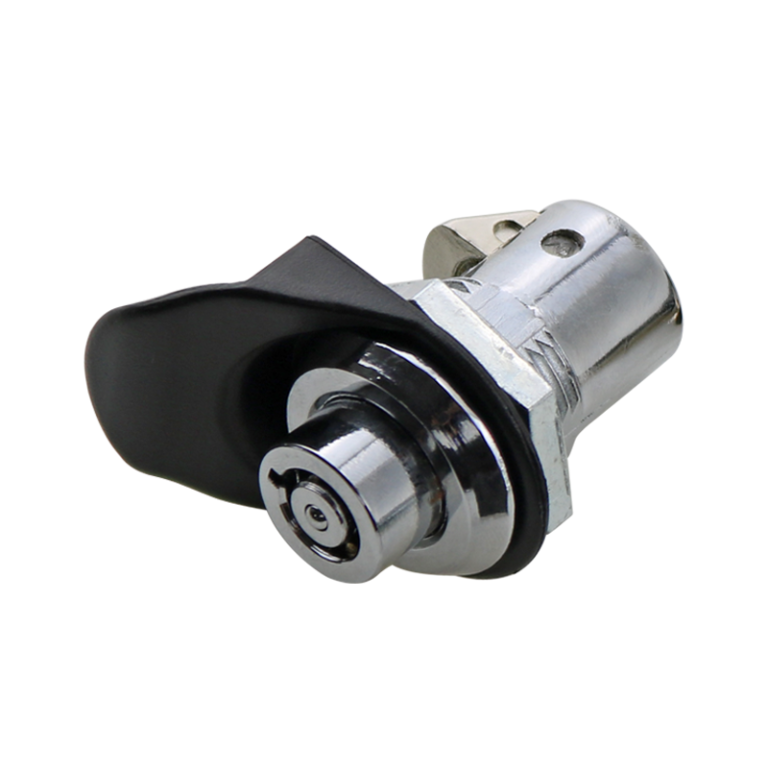
Installation Tutorial
Determine the installation position
Use the measuring tool to confirm the height of the center point of the cam latch from the ground (standard is 900-1100mm). Mark the vertical centerline of the cam latch body and latch hole on the side of the door to ensure that the cam latch body is horizontally aligned with the reserved holes in the door frame.
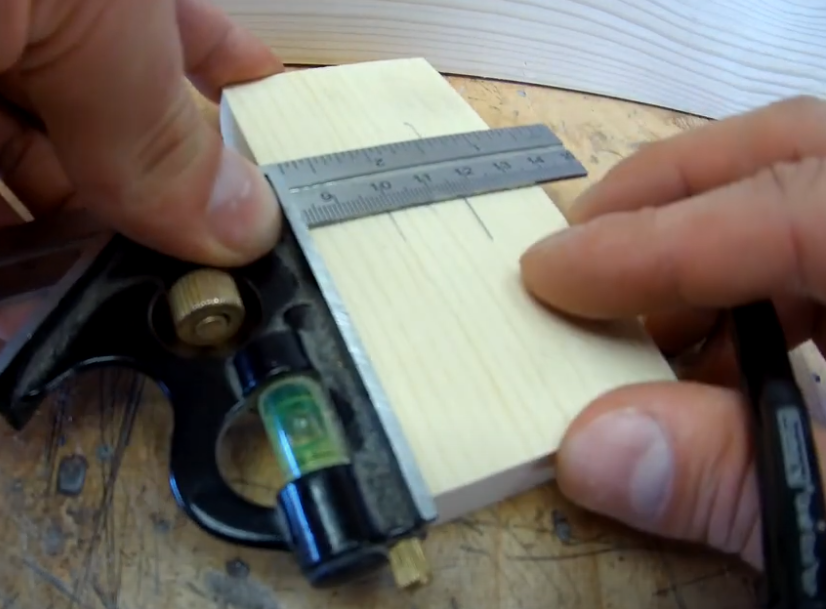
Punching
According to the size of the latch body in the marked position using an electric drill to open the hole:
Drill the slotted holes for the latch body on the side of the door
(The depth is the same as the thickness of the latch body)
Drill holes for the cam along the door edge
(Diameter matching the cam casing).
Drill holes in the door frame for the latch plate
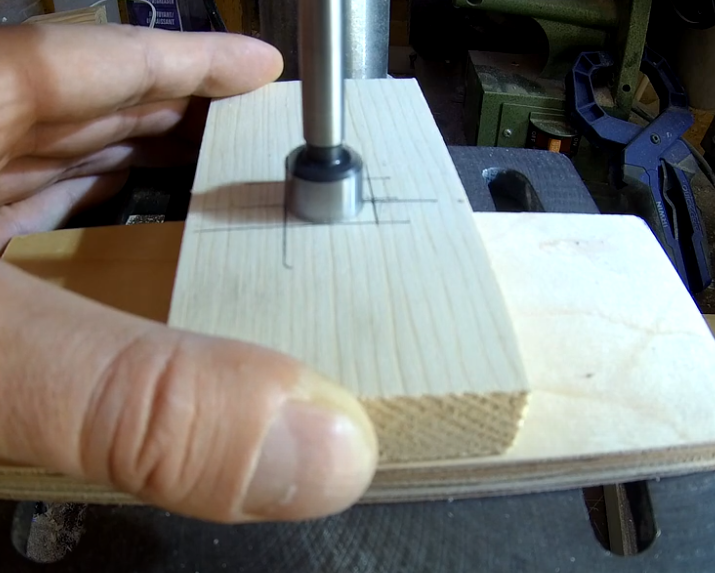
Installation of the latch body
Embed the latch body into the slot hole on the door side and fix it with Φ4mm self-tapping screws through the mounting holes of the latch body. Make sure that the square rod hole of the latch cylinder is vertically aligned with the pivot of the handle outside the door.
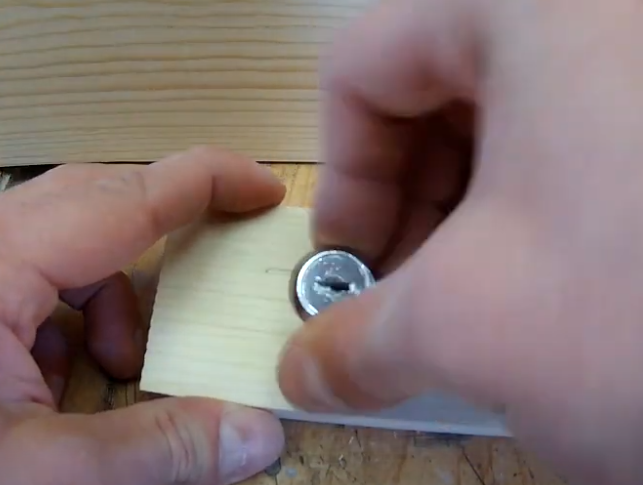
Installation of latch
Insert the latch assembly into the hole on the door side and fasten it with the matching screws. After testing the flexibility of the latch expansion and contraction, install the latch plate of the door frame to ensure that the gap between the door joints is ≤3mm when the latch is fully extended into the plate.
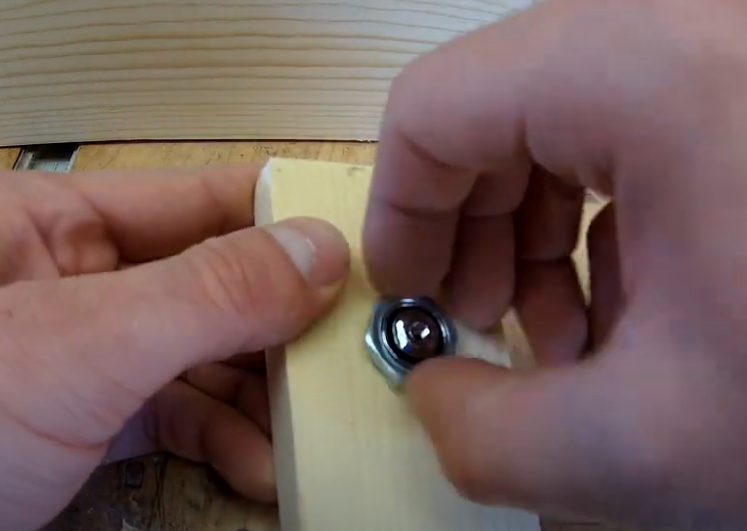
Test and adjustment
Operate the handle to check the latch retraction stroke:
If the resistance is too large
Adjust the tightness of the latch body fixing screws.
When the latch is not fully closed
Fine-tune the horizontal position of the buckle plate.
Test the stability with 10 consecutive switches
Finally tighten all the screws.
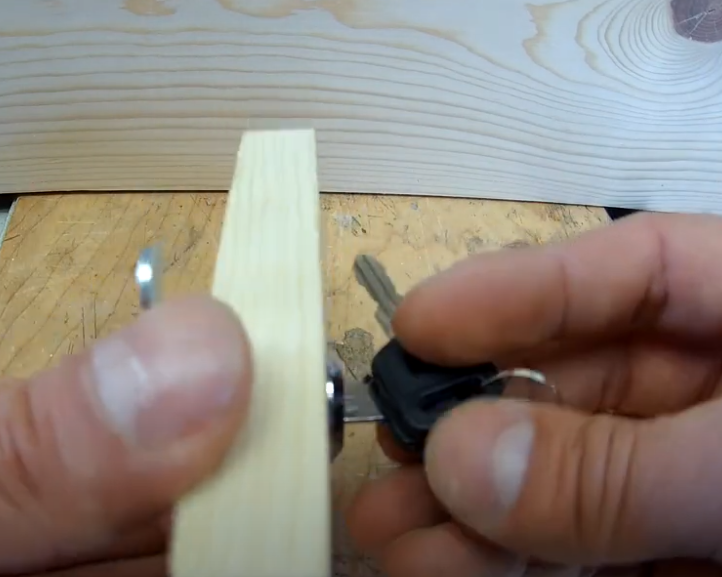
Cam Latch Structure and Working Principle
Explanation of Core Components
Locking head: the operating end that controls the cam rotation angle (key latch or toggle type is available).
Cam Latch: Stainless steel is the best material to generate a compression force of 6-12kg/cm² when rotating.
Anti-tightening nut: models with nylon inserts reduce loosening due to vibration.
Cam Latch Type
Type | Feature | Typical Application Scenario |
---|---|---|
Structure type | ||
Rotary cam latch | Locking by cam rotation, simple structure, direct operation. | Door locks, toolboxes, industrial equipment |
Linear cam latch | Locks with cams moving in a straight line, suitable for compact spaces. | Electronic equipment housings, automobile storage boxes |
Eccentric cam latch | Utilizing the eccentric wheel principle, it provides high mechanical gain and strong locking force. | Heavy machinery, pressure vessel seals |
Mounting form | ||
Surface-mounted type | Fixed directly on the surface, easy installation, no need to cut holes. | Cabinet, control box |
Embedded mounting | Requires mounting holes in panel or frame, flat appearance, high security. | High-end furniture, precision instruments |
Functional features | ||
Unidirectional locking | Locked only when the force is applied in one direction, and can be easily opened in the reverse direction. | Unidirectional pressure vessel, simple door lock |
Bi-directional locking | Locked when force is applied in both directions, strong vibration resistance. | Vehicle-mounted equipment, aerospace equipment |
Adjustable pressure type | Adjustment of locking force is supported to adapt to different sealing or fixing needs. | Laboratory equipment, precision machinery |
Special design | ||
Explosion-proof cam latch | Reinforced structural design, resistant to high pressure or extreme environments. | Petrochemical, explosion-proof equipment |
Concealed design | Cam and operating parts are hidden, simple appearance, high anti-theft. | High-end safe, confidential file cabinet |
Material type | ||
Metal | Steel, aluminum alloy, etc., high strength, corrosion resistance, suitable for heavy-duty environments. | Industrial equipment, outdoor cabinets |
Engineering plastics | Lightweight design, good insulation, low cost. | Household appliances, electronic equipment |
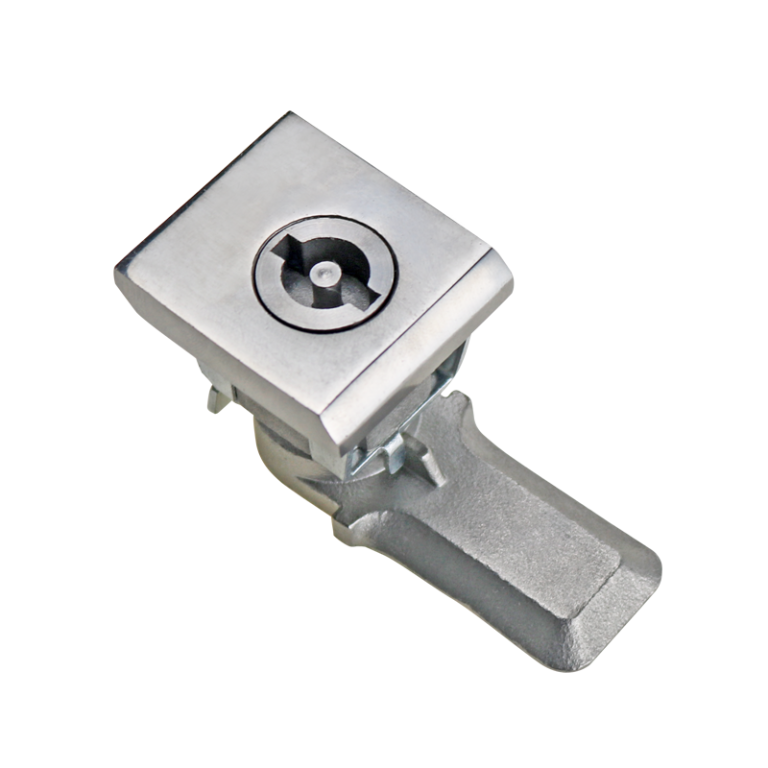
Common Failure Solutions
Still Shaking After Closing
Possible causes: gasket not pressed or cam wear
Solution Steps:
Loosen the nut and re-preload (torque control at 2-3N-m)
Check the cam teeth, wear more than 0.5mm need to be replaced
latch Rust Jammed
Preventive Measures:
Marine environment choose 316 stainless steel
Apply silicone-based grease quarterly (WD-40 is prohibited)
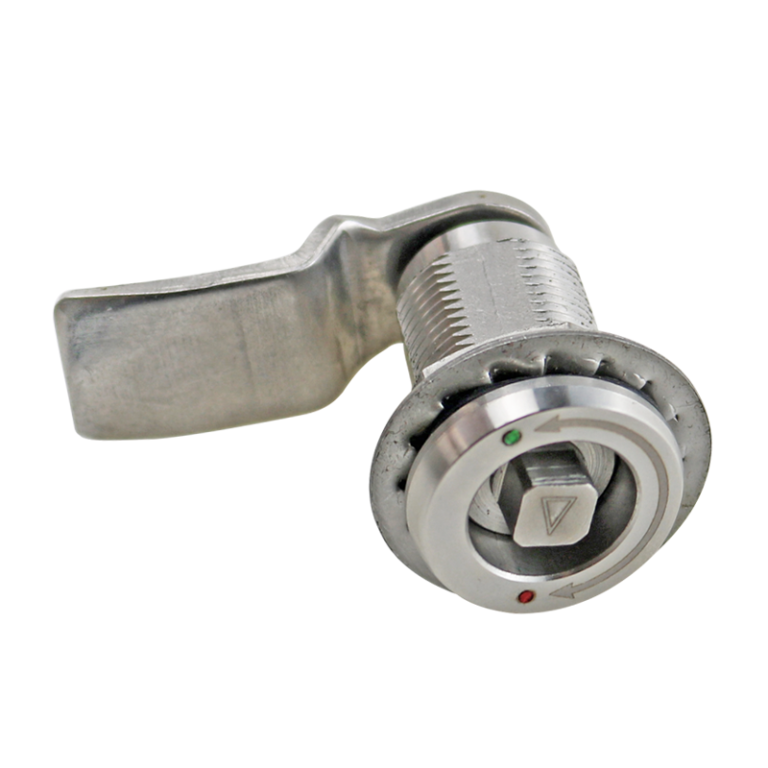
Golden Rules for Engineers
Misoperation-Proof Design:
Uniformly set Cam Latch opening direction clockwise in multi-person work areas
Extreme Temperature Response:
Use nylon washers instead of rubber in environments below 20°C
Electrical Safety Warning:
Tool handles must be wrapped in insulating tape when installing in energized cabinets.
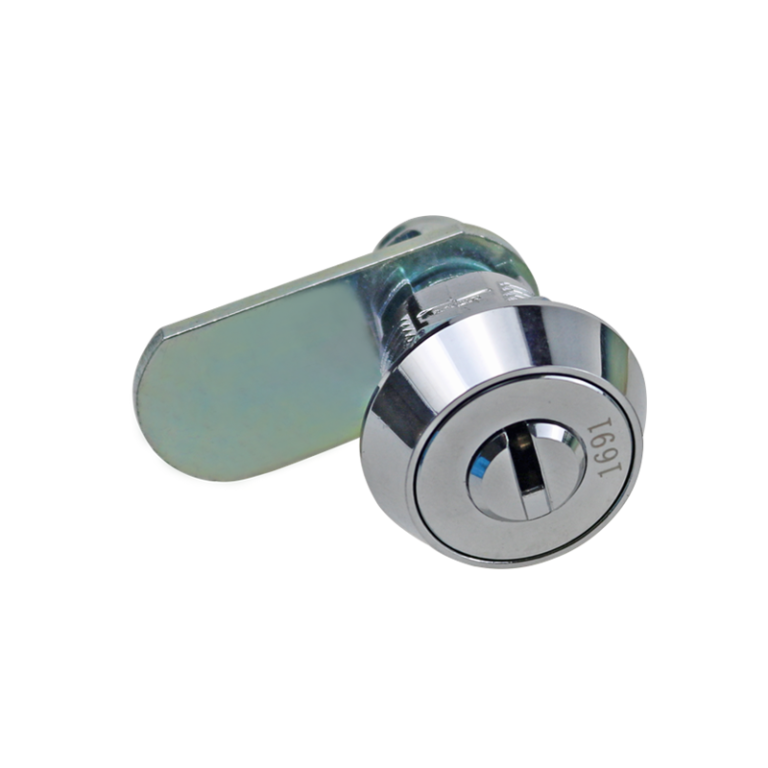
Maintenance Intervals and Replacement Standards
Daily Maintenance Checklist
Weekly: Clean latch contact surfaces with anhydrous alcohol.
Quarterly: check the nut torque value (more than 20% attenuation requires retightening)
Annual: complete disassembly and replacement of all elastomeric components.
Mandatory Replacement Conditions
Visible cracks in the latch body (check with a 10x magnifying glass)
Sealing pressure cannot be reached after 3 consecutive adjustments
Corrosion resulting in >10% reduction in material thickness
Conclusion
Cam Latch installation requires rigorous selection and precise operation, from the opening to the pressure adjustment have clear specifications, combined with regular maintenance and engineering experience, can ensure its long-term stable sealing and reliable latching.