HTAN is one of the leading manufacturers of industrial hinges, handles and latches in China.
-
+86 13720060320
-
julius@haitangs.com

Zinc Alloy Materials: Full Breakdown of Composition, Processes, and Uses
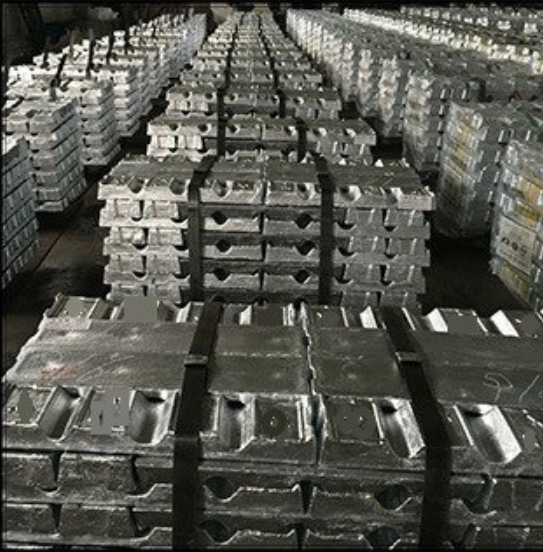
Zinc-based alloys are mainly zinc, adding aluminum, copper, magnesium and other elements, with a low melting point, easy processing, lightweight, corrosion-resistant, platable and other characteristics, widely used in automotive, electronics, industrial hardware and aerospace fields, Zamak / ZA system to meet the diversified needs of the selection of performance, process and corrosion resistance requirements should be taken into account.
Composition and Classification of Zinc Alloys
Core Elements and Role
Element | Common Content Range | Main Role |
---|---|---|
Aluminum (Al) | 3%-27% | Improve strength, hardness and heat resistance, improve fluidity. |
Copper (Cu) | 0.5%-3% | Enhances strength and wear resistance, but high copper reduces ductility. |
Magnesium (Mg) | 0.02%-0.06% | Trace strengthening, grain refinement, improve overall performance |
Nickel (Ni) | 0.06%-0.10% | Enhanced corrosion resistance and high temperature stability (mainly in Zamak 7) |
Tin (Sn), iron (Fe), manganese (Mn) | Trace | Adjustment of castability to control the influence of impurities |
Typical Zinc Alloy Series Comparison
Series | Representative Grade | Principal Composition (%) | Characteristics |
---|---|---|---|
Zamak | Zamak 3 | Zn-4Al-<0.05Mg | Best overall performance, most commonly used |
Zamak 5 | Zn-4Al-1Cu-<0.05Mg | Higher strength and hardness than Zamak 3 | |
Zamak 2 | Zn-4Al-3Cu-<0.05Mg | Higher strength and wear resistance, but lower ductility. | |
Zamak 7 | Zn-4Al-0.06Ni-<0.03Mg | Higher purity and better corrosion resistance. | |
ZA series | ZA-8 | Zn-8Al-small amount of Cu, Mg | High strength die casting, good toughness |
ZA-12 | Zn-12Al-small amount of Cu, Mg | Suitable for heavy-duty castings, improved mechanical properties. | |
ZA-27 | Zn-27Al-small amount of Cu, Mg | Extremely high strength, but slightly poor machinability |
International standard naming system for zinc alloys
Country/Region | Standard No. | Naming Example | Naming Description |
---|---|---|---|
U.S.A. | ASTM B86, B240 | ZP3, ZP5 | Numbered according to major components and properties. |
Europe | EN 1774, EN 12844 | ZL0430 | Z = zinc, L = die casting, 04 = aluminum content of 4%, 30 = copper content of 3.0%. |
China | GB 8738-88 | ZnAl4Cu1 | Identification by element and content |
Japan | JIS H2201, H5301 | ZDC2, ZDC3 | Zamak-like classification system |
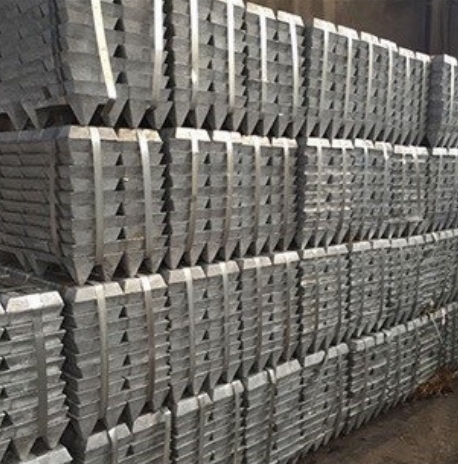
Physical and Chemical Properties of Zinc Alloys
Mechanical Properties
- Tensile strength: 200-440 MPa (higher than most plastics)
- Hardness: 80-120 HB (can be upgraded by heat treatment)
- Elongation: 10-25% (suitable for complex molding)
Thermal Properties
- Melting point: 380-420°C (50% lower than aluminum)
- Coefficient of thermal expansion: 27.4 x 10⁻⁶/°C (design clearance to be considered)
- Thermal conductivity: 110 W/m-K (better than stainless steel)
Electrical and Magnetic Properties
- Electrical conductivity: 28% IACS (28% of pure copper)
- Magnetic conductivity: non-magnetic (suitable for electronic equipment)
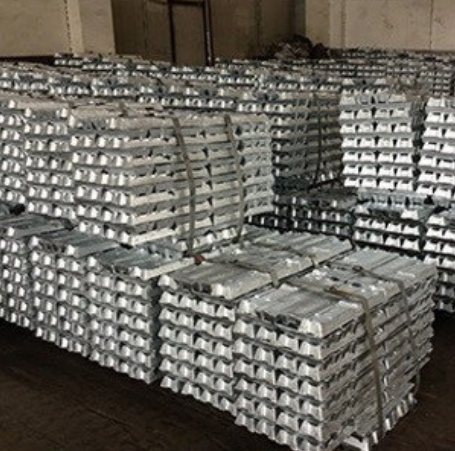
Zinc Alloy Processing Technology
Die Casting Technology
- Temperature control: 410-430°C for molten zinc liquid
- Pressure parameters: 400-1000 bar (adjusted according to part complexity)
- Mold design: draw slope ≥ 1°, wall thickness 1.5-5 mm
Extrusion and Rolling
- Applicable alloys: ZA27 (high aluminum content)
- Processing limitations: deformation rate ≤80% to avoid cracking
Machining
- Cutting speed: 60-150 m/min recommended
- Tool selection: carbide or diamond coated
Surface Treatment and Anti-Corrosion Program
Comparison of Commonly Used Processes
Process | Cost | Salt Spray Resistance Time | Applicable Scenarios |
---|---|---|---|
Chrome plating | High | 500 hours | High-end bathroom hardware |
Nickel plating | Medium | 300 hours | Electronic connectors |
Phosphating | Low | 100 hours | Internal structural parts |
Anti-Corrosion Strategy
- Marine environment: choose ZN series + nickel plating treatment
- Acidic medium: use ZT series + epoxy coating
- High temperature environment: give priority to anodizing treatment

Design and Selection Guide
Structural Design Principles
- Uniform wall thickness: avoid shrinkage (recommended 2-4 mm)
- Rounded corner design: R≥0.5 mm to reduce stress concentration
Balance Between Cost and Performance
- Low load parts: Zamak 3 (15% cost reduction)
- High wear demand: choose ZC1 (1% copper content)
Reliability Test Standards
Typical Applications of Zinc Alloy
Automotive Industry
- Engine mounts
- Sensor housings
Electrical and Electronics
- 5G base station heat sink
- USB Port Housing
Building Decoration
- Door and window hinges
- Outdoor Sculpture
Consumer Products
- Eyeglass frames
- Furniture Handles
Enclosure Fittings
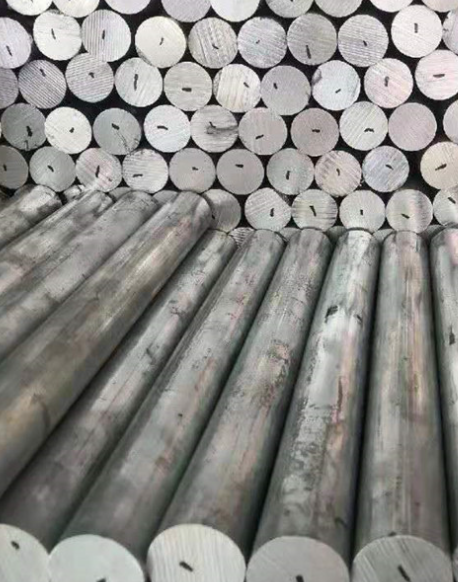
FAQ
Q:What are the key indicators for material selection?
A:Prioritize the mechanical properties, taking into account the mobility and cost control.
Q:What are the mechanical parameters?
A:Zamak 3 basic type vs ZA series high strength alloy performance comparison
Q:What are the key points for safe operation?
A:Finished products are non-toxic, processing requires dust protection and standardized protection.
Conclusion
Zinc-based alloys have low melting point, easy processing, corrosion resistance and good mechanical properties, suitable for automotive electronics and other fields, Zamak/ZA series covers a wide range of needs, the selection of performance, process and corrosion requirements should be integrated.